Formula Student Electric: Squadra Corse Polito
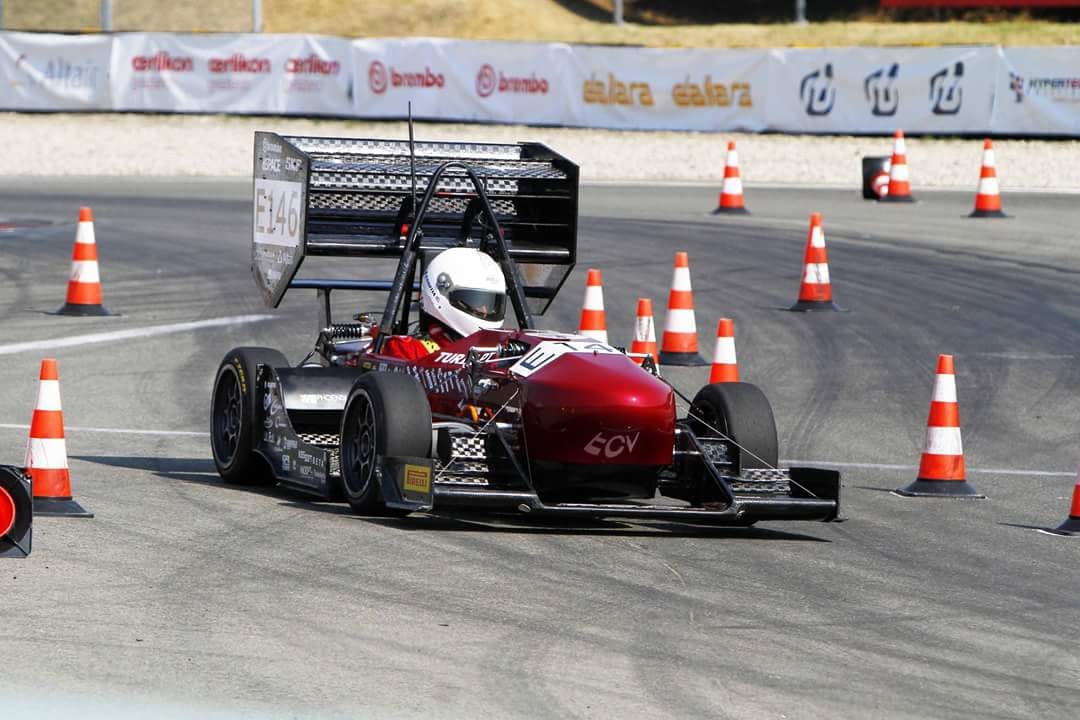
Oct 2017 - Aug 2018 · Turin, Italy
In the second year of my Masters in Turin, I was honored to be part of the Squadra Corse Polito Team for the 2017 - 2018 Formula Student Electric season.
I became part of the Unsprung Masses division during the design phase of the new SC18 Integrale car. My task was to design the wheel uprights and the brake rotors.
A Motorsports experience, or close
I had only recently learned "formally" (i.e. at a university course) about Numerical Modeling and Simulation. My previous knowledge from Venezuela was more theoretical on Solid Mechanics and Machines Design, and lots of online tutorials about FEM analysis.
Now we were talking about mesh element types and linear vs parabolic formulations for deformation and stress computations. I was very excited because those were some of the reasons I chose an Automotive Engineering Masters course in the first place.
This is when I got to use industry-level FEM analysis tools like Altair Hyperworks and Ansys Workbench outside of a class project. The team worked on CATIA V5, which was also new to me. For some of the guys, Solidworks (which I had been using for both CAD and FEM for the last 5 years) was a kid's toy for drawing in 3D and bending things for fun. Not that I share their view, but it was exciting to learn new things.
I got really interested in optimizing the structure of the wheel uprights, and the goal was achieving a 15% mass reduction with a maximum variation of 0.1° of camber and toe compliance. However, coming from Formula SAE UCV, I had learned to be pragmatic, so I decided to follow two approaches:
- Simulate the stresses on the uprights using realistic constraints based on the stiffness properties of the wheel bearings. Fancy simulations would not tell anything usable if based on poor constraints.
- Create the geometry with DFMA in mind. This way, even if we had access to a 5-axis CNC mill, machining operations wouldn't be much of a pain or back-and-forth revisions with the machinists.
Not to brag, but I'm proud to say that the final uprights were not designed from a topological optimization, and yet they were 15% lighter than the ones from the previous season (hey, -150 grams x 4 parts!) whilst being 70% more rigid in terms of suspension points displacement under load and bearing seat deformation. This last point was in part because the motor we used was more compact.
Comparison of Signed Von Mises element stresses and deformation between previous uprights design (left) and the new one (right).
Later on, while finishing the design and starting the prototyping and testing phase, I became the division leader.
It was a ton of work, but I was happier than ever making sure the designs for all subassemblies (suspension, steering, brakes, wheel uprights) were correctly integrated and worked properly with the designs from other divisions.
I also had to check with my colleagues the compliance with FSAE regulations, oversee the design and cost reports, and help with the manufacturing specifications and assembly of the car. Then giving support and collecting data during track test sessions.
At the team, we were few (~15) working full-time, and we wore many hats, despite what our "role" was. It was a team of volunteer students, after all.
Since I had previously freelanced doing renderings of consumer electronics, I took the chance to create some eye candy using the CAD assemblies of Desy. These proved useful when preparing the Design presentations for the competition.
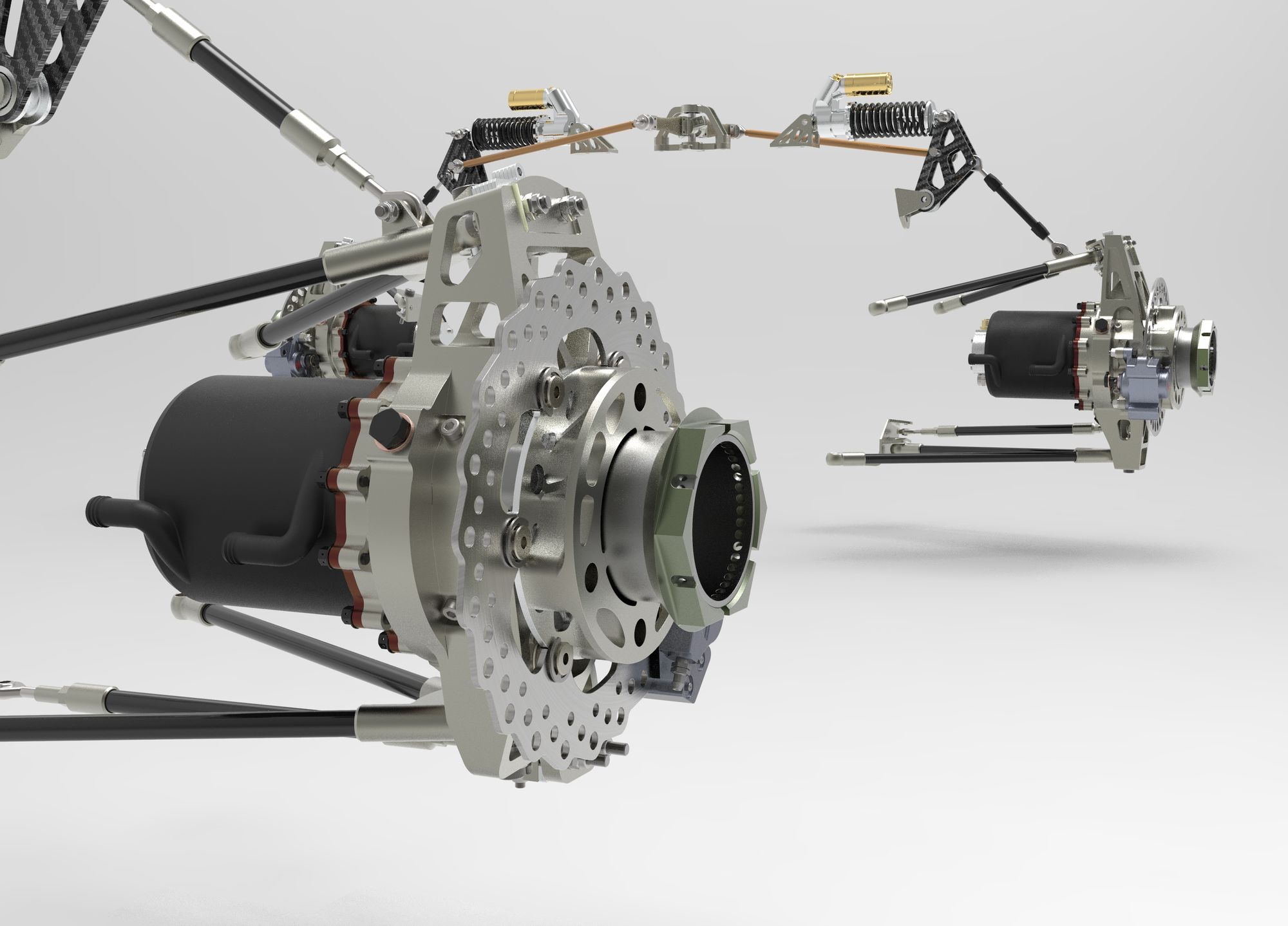
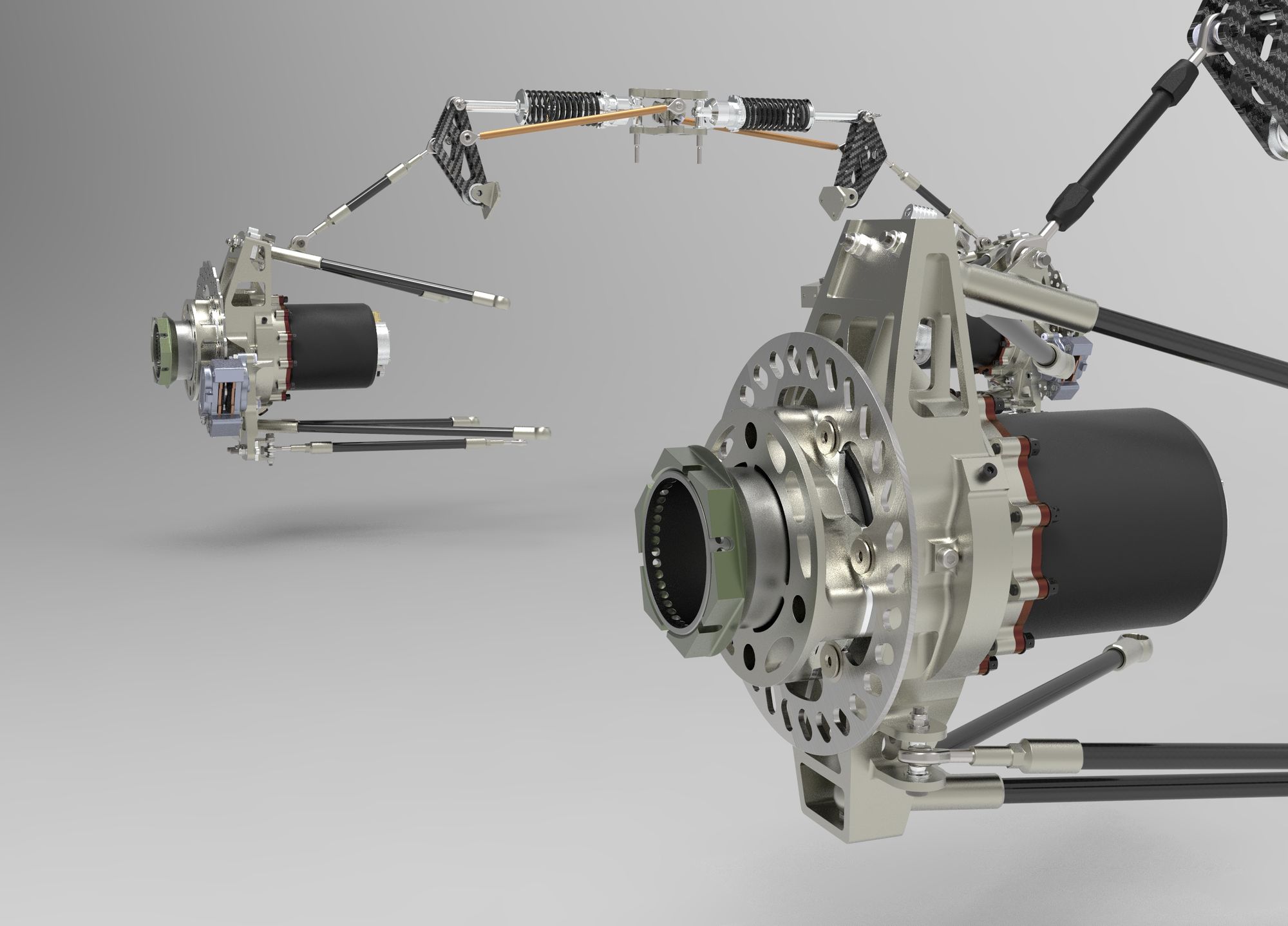
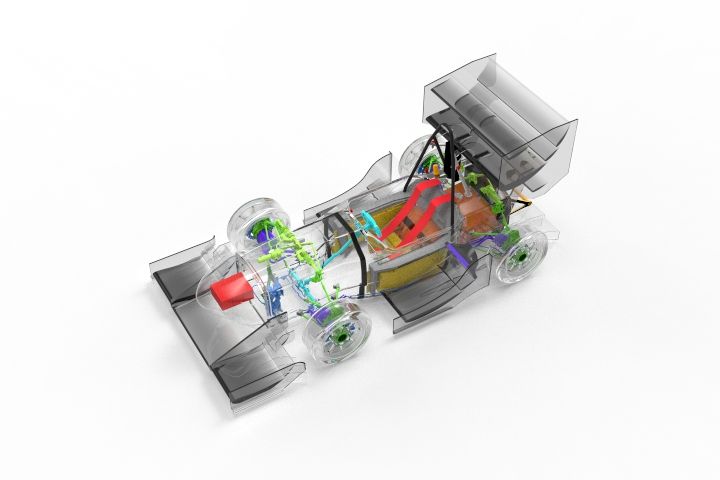
Left and center: Renderings of the unsprung mass assembly. Right: vehicle subsystems of SC18. Created in Keyshot 7.
Overall Squadra Corse was quite a rewarding experience.
I really enjoyed being part of the team and building an electric race car from scratch. I got to collaborate with incredible people and grow as a person and as an engineer.
We achieved 3rd place in the Formula SAE Italy 2018 competition, and 13th in Formula Student Spain 2018. Although we didn't win, I won't forget all the happy moments with the team during the long hours at the workshop and the test track when designing and building Desy.
After Squadra Corse
Squadra Corse opened many opportunities for me as an Engineering student.
Some of them I didn't catch or didn't appreciate fully at the time, while others determined the path I'm currently in.
After the FSAE Italy competition in 2018, I received a proposal to work as a consultant at Ferrari Spa within the Durability and Reliability testing department. Being a young kid full of dreams, I accepted, of course.
My journey with data-driven problem-solving started right there - though I didn't notice at first.
Other than developing my excessively broad and extensive MSc. Thesis about the work I did as part of the team, I have written a few articles related to this experience:
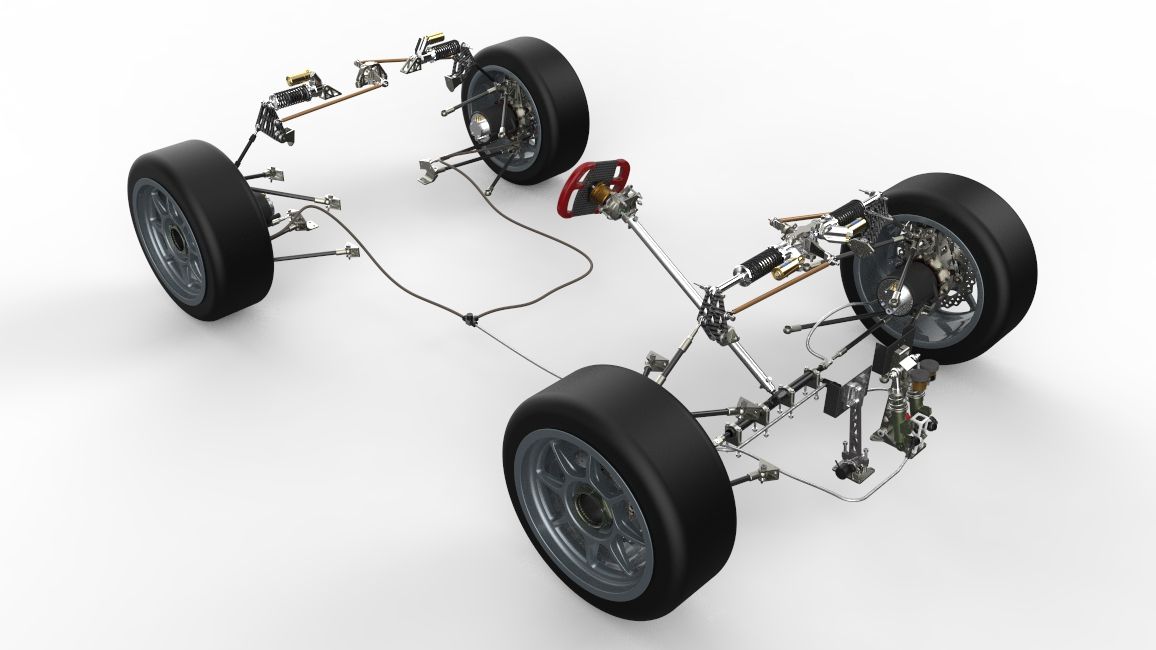